Google’s Distinctive Headquarters and Bemo’s Engineered Solution
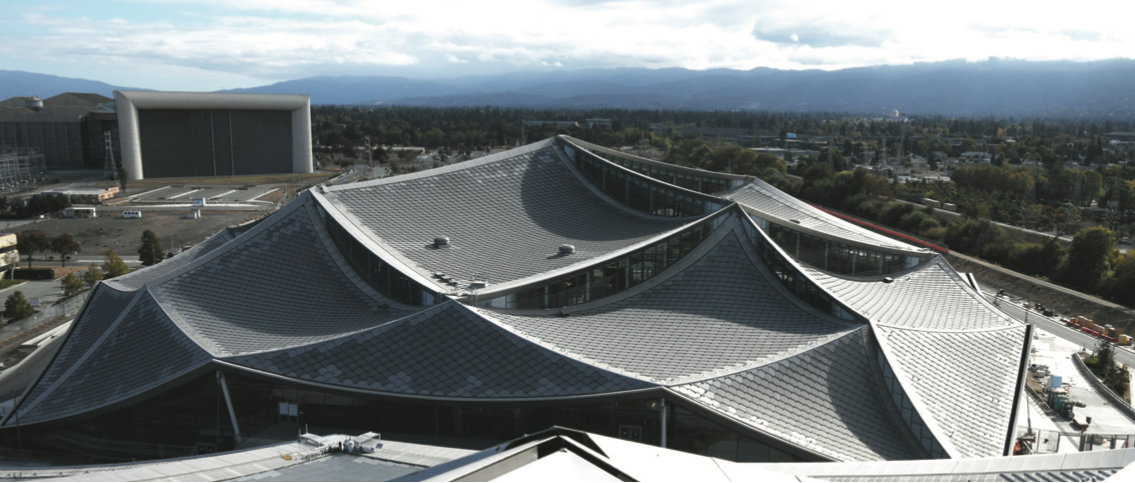
Google Mountain View, CA Corporate Headquarters Four Building Complex On 2 Separate Sites
Google is in the final phases of building two new campuses in Mountain View, CA. One at Charleston East (in the midst of their current HQ campus) and the second on NASA’s Moffett Field a couple of blocks away. Unlike the existing buildings it now occupies, these new multi-building complexes are visually striking, skyline changing and an engineering challenge on almost every level. The new Google buildings join other notable mega-companies in the area that are not only transforming technology and communications but also building one-of- a-kind architectural landmarks.
The Bay View structures are part of the multi-building complex located on NASA’s Moffett Field while the Charleston East Campus has one large central structure. These four structures are as unique in design and engineering as any in the area. The erected steel and the roof canopies soar to over 160 feet above the ground. The roof systems collectively are comprised of one-hundred twenty (120) massive, individual concave squares, triangles, kite shapes and rectangles (called canopy bays) that seem to drape gracefully downward like enormous organic leaves. Between the different levels of these canopies are glass clerestories that allow natural light into the workspaces. Looking up from the inside, the flowing roof levels and steel superstructure of the overhead canopy evoke the feeling of being inside a giant tent structure.
The unique architectural roofline design has created engineering, manufacturing and construction challenges. The concave shape of the roof surfaces was architecturally designed as segmented decking.

By the Numbers – Google Charleston East and Google Bay View (4 Buildings)
- 400mm .040" Aluminum BEMO Panels - 949,376 sf | (88,232 m2)
- Number Of Individual Roof Areas (Canopies) - 120 each
- Panel Thermal Halter Clips - 194,740 each
- Panel Fixed Point Aluminum Halter Clips - 48,204 each
- BEMO-Flex Base Track Sections - 271,824 lf | (82,873 m) | 83,099 tracks | 51.48 miles
- BEMO-Flex Upper Track Sections - 300,396 lf | (91,584 m) | 83,099 tracks | 56.89 miles
- BEMO-Flex Supporting Height/Pitch Saddles - 249,954 each
- Deckfast Fasteners - 790,654 each
- Tek-3 Fasteners - 1,022,704 each
- Bulb-Tite Rivets - 999,816 each
- Holes Punched Into Flex Systems For Assembly/Installation - 18,062,091 each
- Unique Part Number Engravings - 25,417,452 hits
- Individual Models And Layouts - 240 each
- Pre-Scans, Setting Out Surveys, As-Built Scans - 360 each
- BEMO-Akkord Rails - 504,747 lf | (153,886 m) | 95.60 miles
- Hll Fall Safety System - 73,212 lf | (22,321 m) | 13.87 miles
- Hll Posts With Base Plates - 5,625 each
- Bemo Walkway Assemblies - 31,160 lf | (9,500 m) | 5.90 miles
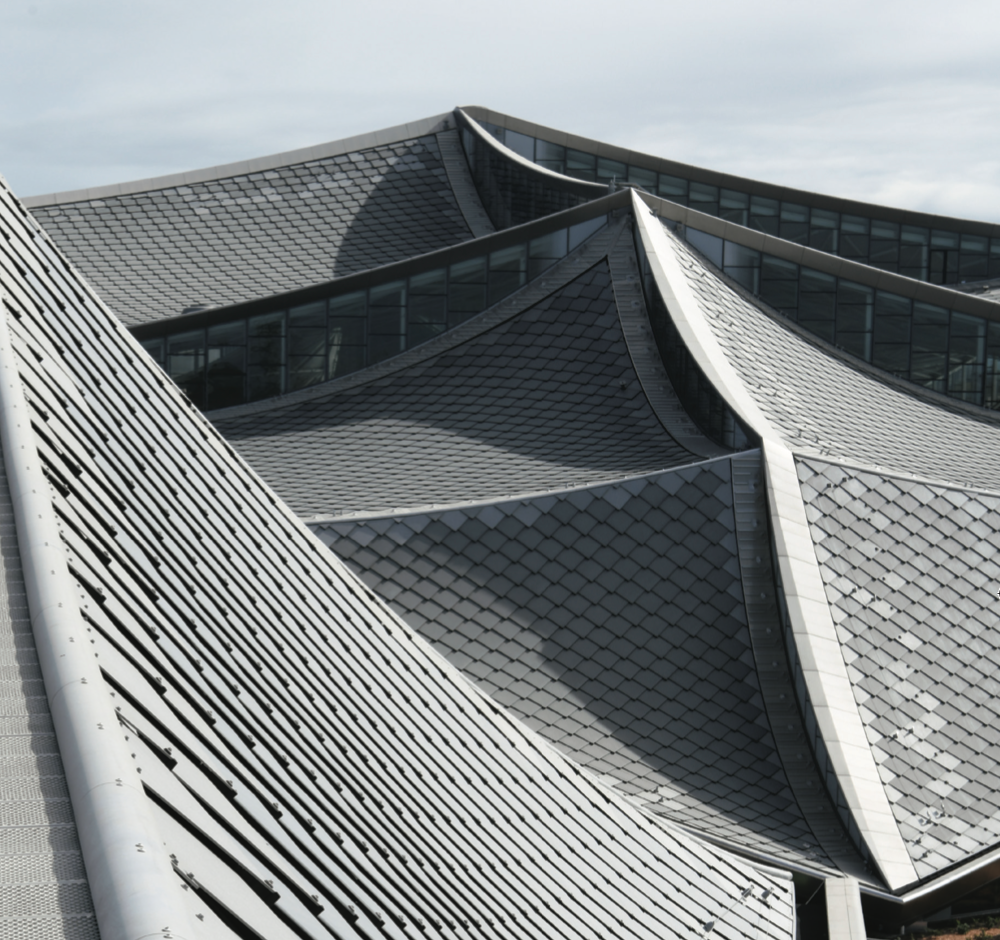
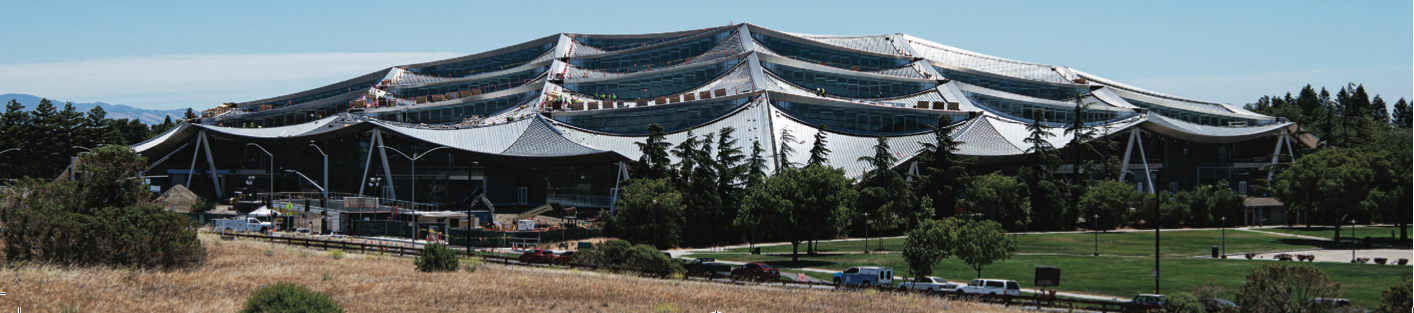
structures attached to curved steel truss systems. To accommodate the surface delamination, (which is the difference between the actual location of the segmented and deflected steel structure and the theoretically desired finished location of the roofing panel system), a constructible and efficient system had to be employed to reduce the overall structural steel costs. Because of the faceted and undulating structure below, our unique and specialized solution was used to attach the standing seam roof. Bemo USA Corporation’s proprietary and patented BEMO-Flex Substructure system is the unique solution.
To meet the engineering, performance and manufacturing challenges, Bemo USA invested in specialized CNC machinery and bespoke software to produce the mass-customized attachments points and metal standing seam panels. The comprehensive system enabled the efficient and accurate production of more than 260,000 unique clip attachment points providing structural connections while each one adjusted in three-dimensional, height, pitch and angle orientation. To ensure that every BEMO-Flex connection point was accurate, 3-D and Total Station scanning provided precise field locations and measurements. Bemo had a full team of field surveyors that worked for over 18 months on the projects. Bemo computational design engineers evaluated the individual data points and matched those points up to the desired design surface location. Specialized computer modeling algorithms are used to create the individual BEMO-Flex CAD details. Then, using the modeled data, precision components were manufactured and assembled on multi-clip tracks. Each completely unique track was produced in an assembly line style manufacturing process. These processes alone required over 43.4 million precisely located holes and engraved identifiers to be included in the manufacturing processes.
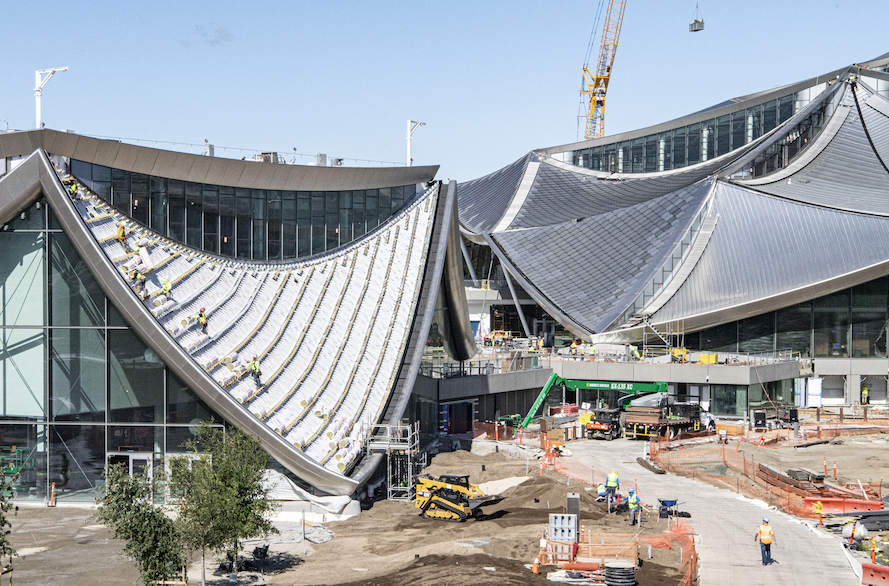
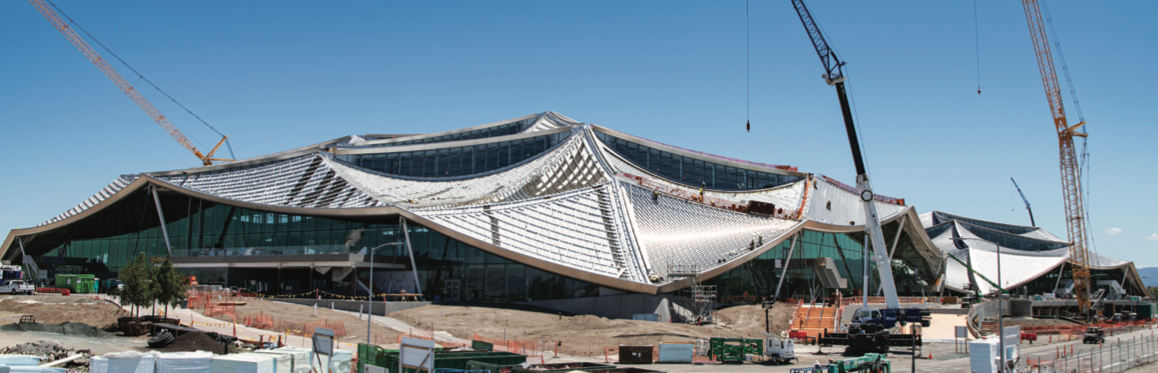
BEMO-Flex Freeform Architecture, Parametric Design For Smooth Flowing Graceful Lines
To meet the engineering, performance and manufacturing challenges, Bemo USA invested
in specialized CNC machinery and bespoke software to produce the mass-customized attachments points and metal standing seam panels. The comprehensive system enabled the efficient and accurate production of more than 260,000 unique clip attachment points providing structural connections while each one adjusted in three-dimensional, height, pitch and angle orientation. To ensure that every BEMO-Flex connection point was accurate, 3-D and Total Station scanning provided precise field locations and measurements. Bemo had a full team of field surveyors that worked for over 18 months on the projects. Bemo computational design engineers evaluated the individual data points and matched those points up to the desired design surface location. Specialized computer modeling algorithms are used to create the individual BEMO-Flex CAD details. Then, using the modeled data, precision components were manufactured and assembled on multi-clip tracks. Each completely unique track was produced in an assembly line style manufacturing process. These processes alone required over 43.4 million precisely located holes and engraved identifiers to be included in the manufacturing processes.
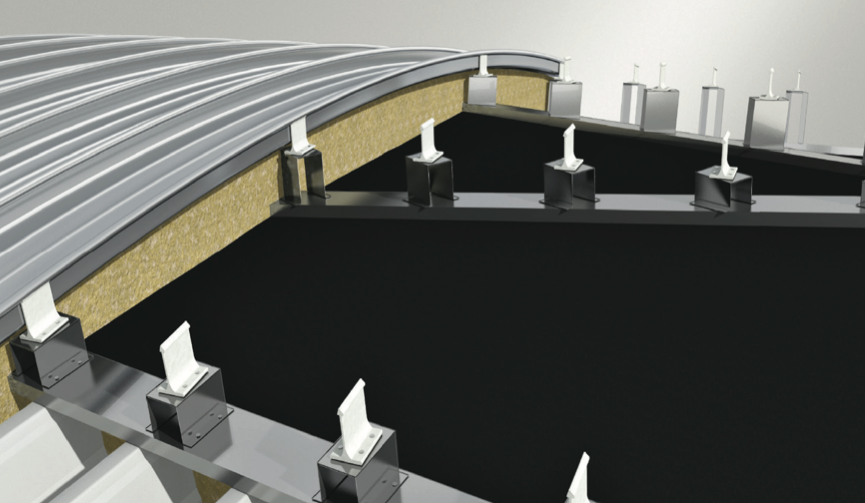
The new Google campuses are covered with over 949,000 sf (88,232 m2) of BEMO N65 400 .040" mill-finished aluminum standing seam roof panels. Very much like the BEMO-Flex system of mass-custom manufacturing, each roof panel is unique in length, curve radius, aluminum alloy, and thickness variations. Roof panels run from just a couple of feet long to over 127' (39 m). Almost all of the roof panels are curved. The longer panels naturally curved as they lay down on the concave structure. Other shorter panels or those with a tighter radius were mechanically curved and craned to the roofing areas. Mechanically curved panels used the same modeling data that was generated for the precise manufacture of the BEMO-Flex system. After the custom standing seam roof panel was roll-formed from the BEMO Mobile Factory Mill, data from the BEMO-Flex modeling was entered into a computer-controlled Bemo curving mill. The panel passed through the curving mill, where a combination of the digital processor and the skilled hand and experience of the operator curved the panels to exact specifications ready for installation. Of the 949,000 sf (88,232 m2) BEMO N65 panels, 200,000 sf (18,500 m2) were factory-formed and shipped to the site and, 749,000 sf (69,584 m2) were field-formed on-site using the BEMO-Mobile Factory Mill in Mountain View, California.
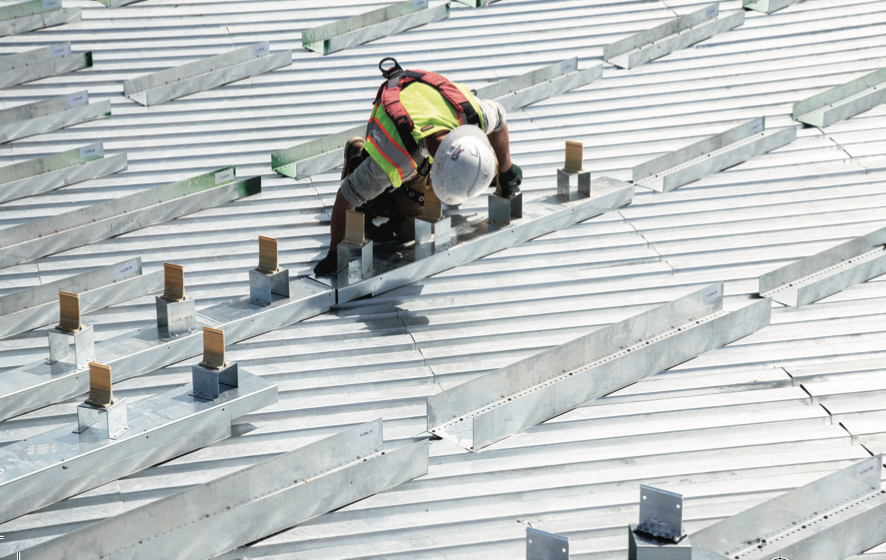
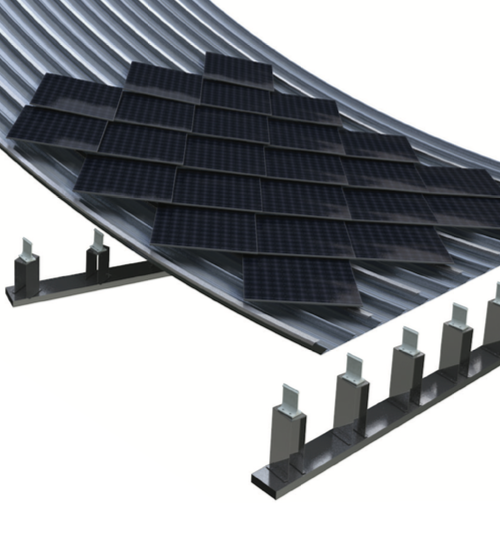
BEMO-Flex Provides Multi-Axis Attachment Points To Control Height, Angle And Pitch
With the BEMO-Flex system, Architects and owners can achieve the graceful lines and parametric design they desire at a much more economical cost. The BEMO-Flex system for BEMO standing seam metal roofs provides multi-axis attachment points. This controls each clip attachment’s height, angle, and pitch for a segmented or “out of plane” deck, all while reducing labor costs and increasing construction efficiencies.
BEMO-Flex allows precise, high-quality, and affordable application of complicated roof and wall systems. Explicitly developed for BEMO standing seam metal roof panels and wall systems, the BEMO-Flex rail modules provide the solution of achieving smooth surface lines.
Through combined use of project surface and deck models, 3-D and Total Station scan, proprietary software, and the latest generation manufacturing processes, Bemo offers this mass-customized system within such a short duration that it meets even the most aggressive construction schedules. The typical lead time from scan to products ready to ship is only a few weeks.
The BEMO-Flex system can also be applied to retrofit applications where an existing structure needs a new weather surface, an air-space for additional insulation, and a desire to increase roof slope to change the final visual lines.
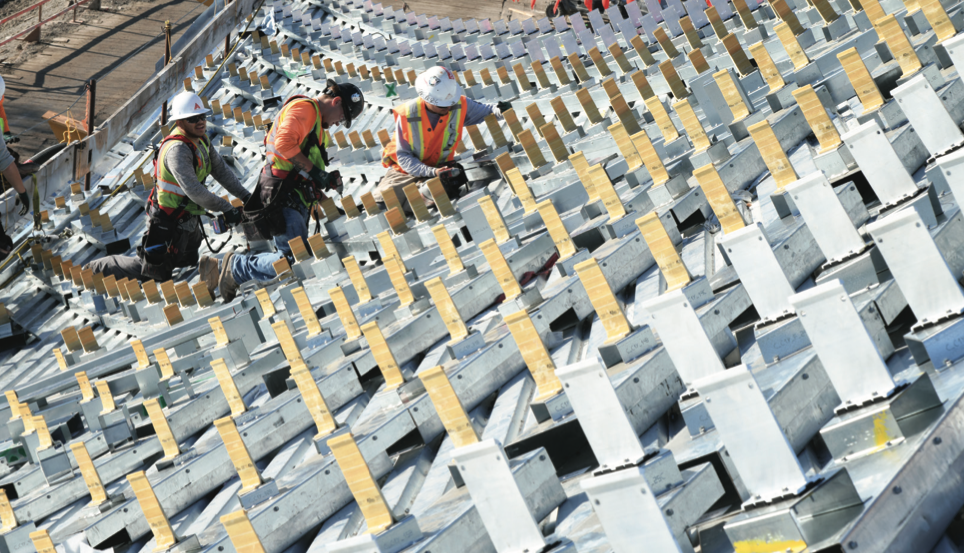
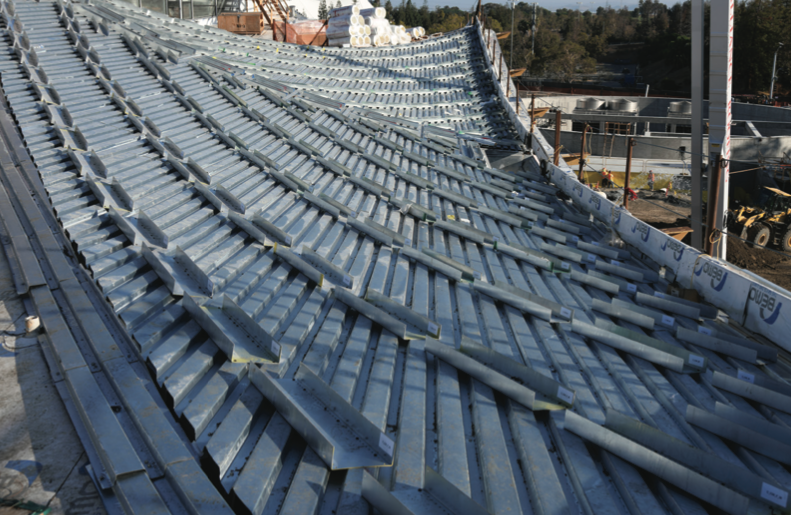
BEMO Walkway and Horizontal Life Line (HLL) Fall Safety Without Roof Penetrations
Safety is an ongoing concern during the building process and continuing maintenance. Bemo USA designed an assembly that incorporates walkways and fall safety as a single composition, a first-of-its-kind HLL (horizontal lifeline) system.
It is normal to have HLL systems installed on the Bemo structural standing seam metal panels with clamps but, attaching them directly onto the walkways is an engineering innovation. The HLL system and walkway assemblies work as a single unit in combining maintenance worker foot-traffic zones with the fall safety system. The design team's challenge drove this decision to free up as much of the roof area as possible for photovoltaic panels (PV). However, doing so changed the load path the force sends through to the structure during deployment. That being the case, full-scale dynamic load testing of the entire walkway and fall safety assemblies was required. The result is that Bemo successfully engineered a complete system that meets the project and CAL-OSHA requirements, all without ever penetrating the standing seam roof panels.
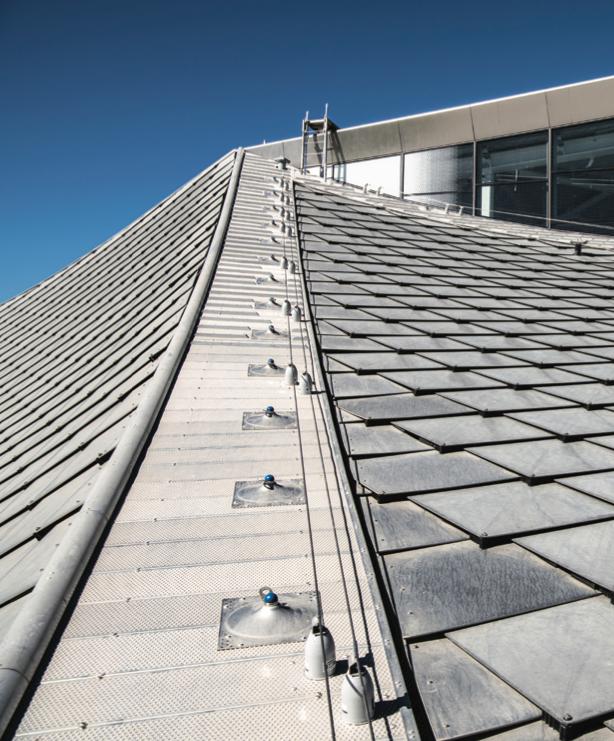
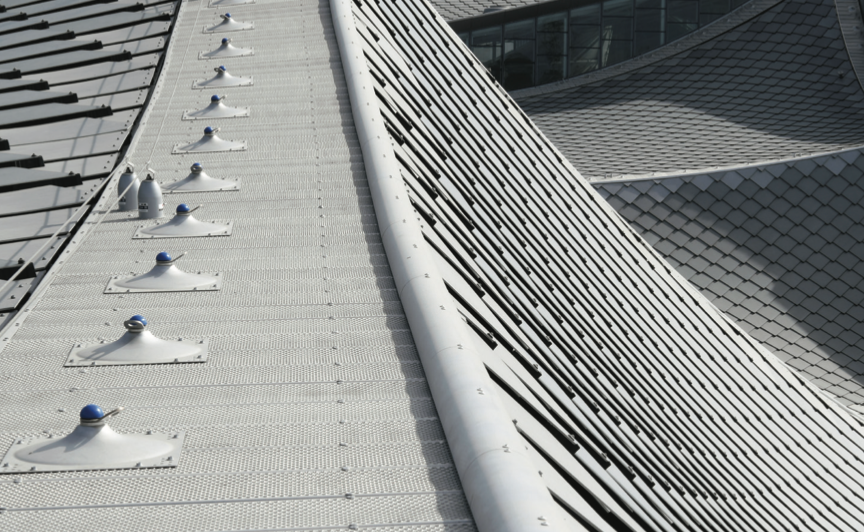
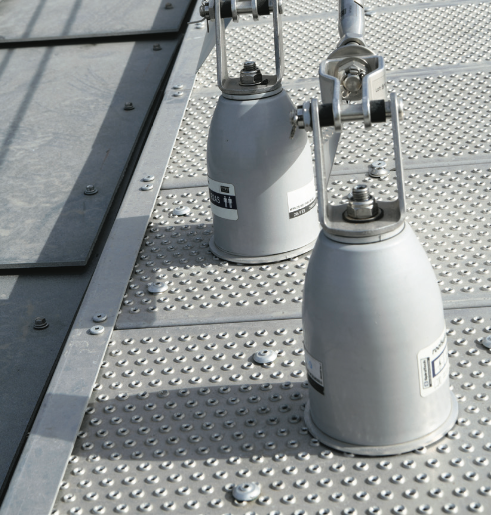
BEMO-Akkord Rails – Photovoltaic Attachment
Google installed more than 90,000 photovoltaic panels (PV) on the roof to generate up to 7 megawatts of electricity as a first-of-its-kind dragon-scale solar skin. The BEMO Roofing system intentionally avoids penetrations of the weather area. With the BEMO-Akkord rail system, all the PV panels were installed without a single hole being cut in the roofing assembly. Bemo provided over 504,747 lf (153,886 m) of straight and custom curved BEMO-Akkord rails.
BEMO-Akkord rails are designed to attach PV panels to BEMO Roof standing seams without penetrating the roof. Because of the long convex curved shape of the roof, many of the BEMO-Akkord rails required custom curving.
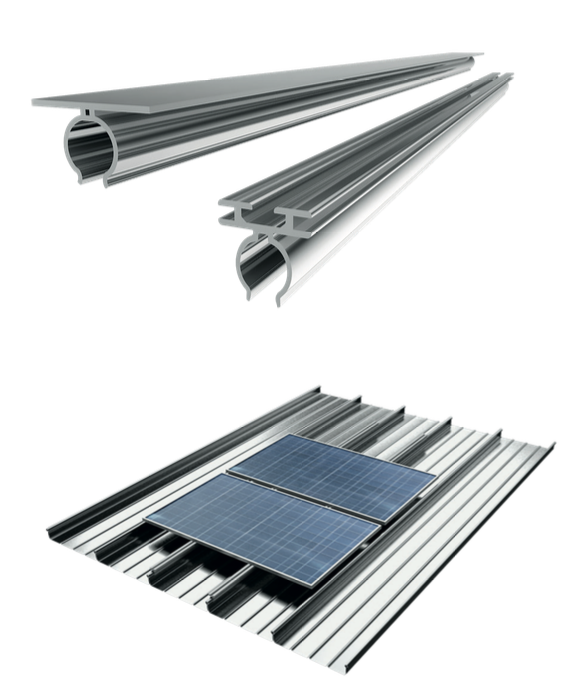
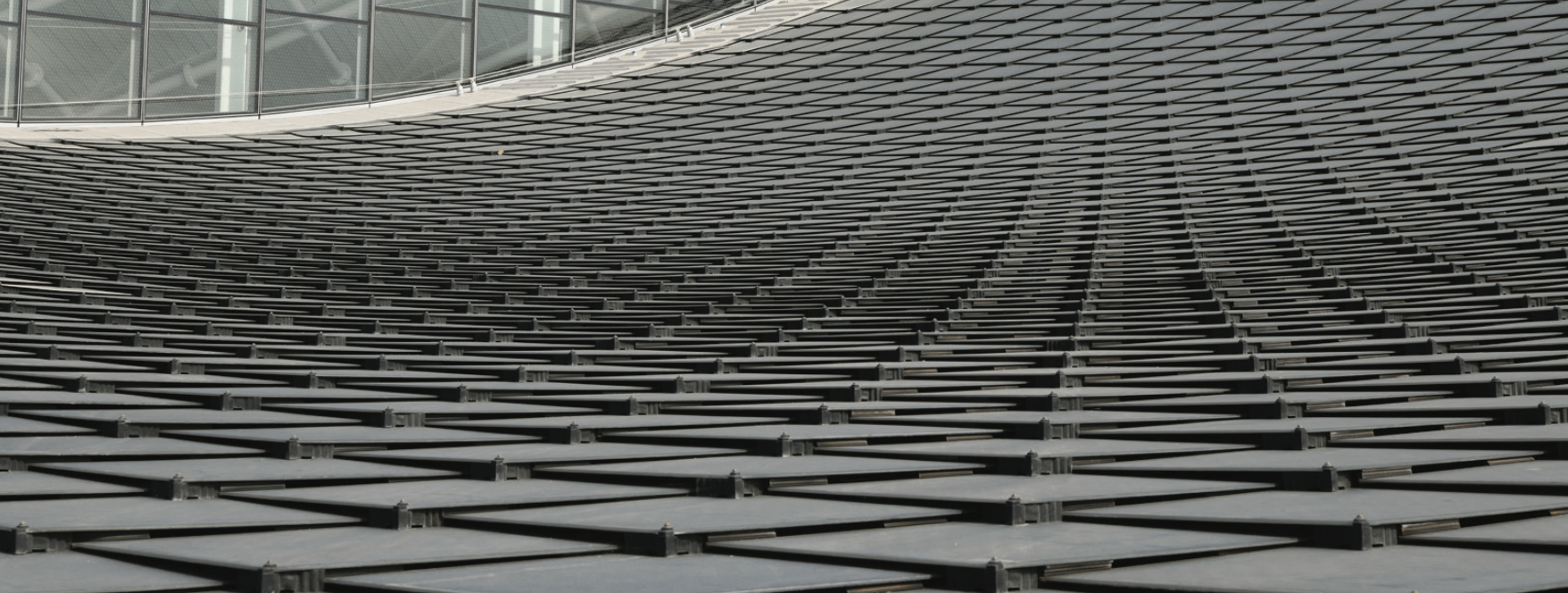
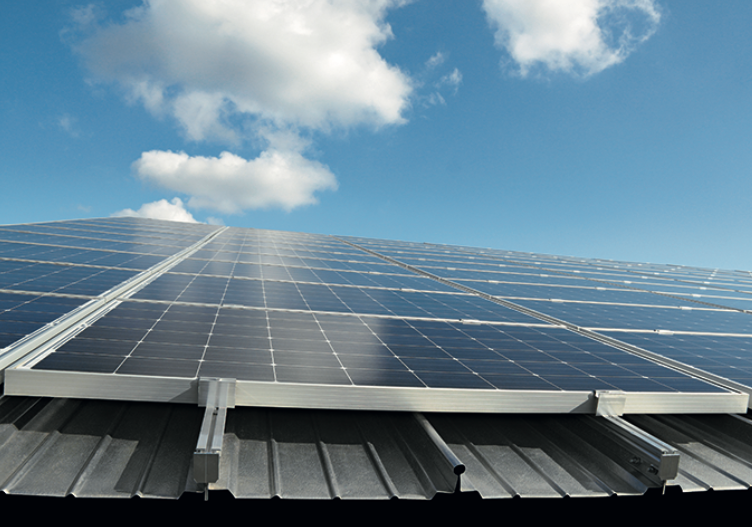
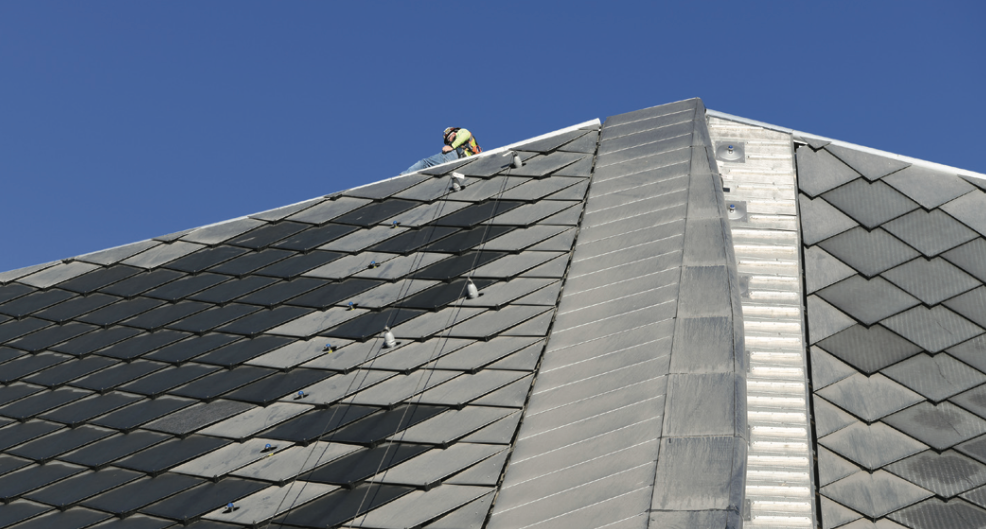